- Home
- Special Services
MARINE SERVICES
construction
other services
weld services
- NDT Services
methods
additional services
- About Us
- Locations
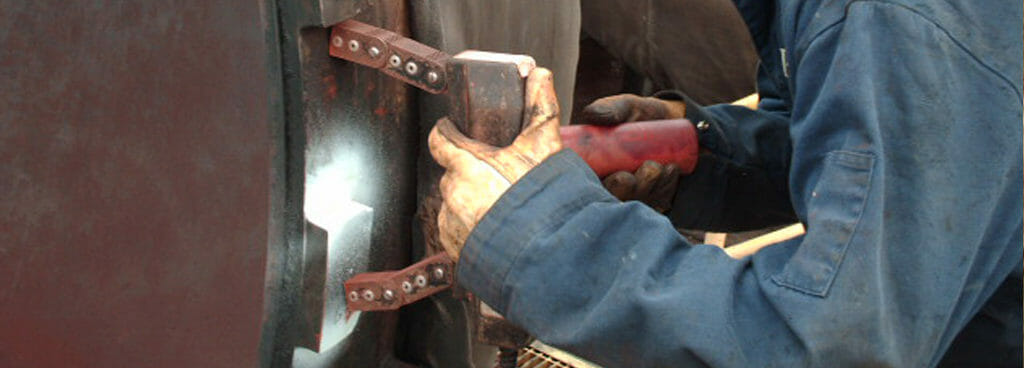
Importance of Regular Inspections
International Inspection performs a variety of NDE inspection services for clients in a variety of industries. Otherwise known as nondestructive examination, NDE is a broad category of services that assess the characteristics of materials, assemblies, equipment, and structures without causing long-term damage to the subject of analysis. Technicians use these methods to give indications of any existing defects that could undermine the asset’s performance.
Our technicians bring their years of experience to every job, drawing on their great familiarity serving a wide range of industries to provide expert analysis. These ASNT-certified inspectors are comfortable using a variety of nondestructive methods to assess the conditions of storage tanks, pressure vessels, piping systems, and other industrial assets. As these structures age, they get compromised as a result of exposure to environmental weathering (corrosion), cyclical stresses (fatigue), and other forces associated with their intended service conditions. This subtle, often gradual deterioration can cause a loss of functionality, leading to reduced productivity and potentially working hazards. Clients thus need to maintain oversight of their equipment’s health to avoid failure resulting in costly downtime, repairs, or injury to personnel. Our inspection services can help in this regard.
By scheduling regular inspections of their industrial assets, clients can take a proactive step to prevent unwelcome surprises. Our team of highly qualified technicians performs thorough inspections compliant with a variety of codes to this effect. They examine industrial assets for the many indicators of damage and reduced performance by using a host of nondestructive testing methods.
Our Methods of NDE Inspection
Our certified field inspectors are experienced at assessing different material types and weld processes. They perform NDE inspection services using a methodical approach, employing any of the following methods as relevant to the scope of their inspection:
Visual Testing (VT)
Visual testing is the most fundamental of nondestructive testing methods. Trained inspectors pore over areas of interest to locate any symptoms of damage visible from the surface of the equipment. These efforts may be supplemented by specialized cameras to either access otherwise hard-to-reach locations or record footage for reporting. Depending on the results of their initial findings, technicians may perform additional testing to characterize the nature and extent of defects discovered during this phase.
Penetrant Testing (PT)
Penetrant testing (also referred to as liquid penetrant or dye penetrant) is a method used to find surface level discontinuities in a non-porous material. By administering and then removing a chemical agent, our technicians can highlight minuscule cracks, fractures, porosity, and other defects. We may use an array of penetrant types depending on the needs of the client or circumstances of the test, including:
- Solvent-removable variety for small areas of analysis — results examined under ambient white light
- Hydrophobic variety for large areas and materials sensitive to chemical reaction with solvent-removable — results examined under ambient white light
- Fluorescent variety for increased sensitivity and improved visibility — results examined in dark conditions with ultraviolet light
Magnetic Particle Testing (MT)
Magnetic particle testing locates discontinuities at and near the surface of ferromagnetic materials. By applying a magnetic field to the equipment and then utilizing ferrous particles, our technicians can produce visual indications of defects in the subject such as cracks, laminations, and cupping. Performing this method takes little time and yields useful results in a range of testing conditions. Inspectors may employ either dry or wet particles depending on the scope of analysis, with:
- Dry particles being most commonly used for field analysis
- Wet particles being more sensitive and thus yielding indications for smaller discontinuities
- Wet fluorescent particles making indications more visible at the cost of needing dark conditions and ultraviolet light for analysis
Ultrasonic Testing (UT)
Ultrasonic testing uses sound waves to establish a variety of subsurface characteristics, including:
- Thickness Measurements
- Bond Testing
- Locating defects like cracks, delamination, stringers, etc.
We provide two different types of ultrasonic analysis based on the needs of the client. The first of these, referred to as the pulse-echo technique, allows technicians to measure the material thickness of metal substrates without having to first remove their protective coating layers. The second type is useful for monitoring conditions over time in an area of interest that may be susceptible to corrosion; it enables inspectors to produce a cross-sectional image of the subject, featuring the shape, depth, and location of discontinuities.
Radiography Testing (RT)
Our field inspectors perform radiography testing with modern projectors that use Iridium 192 isotopes, which are less radioactive than the standard Cobalt-60. This team travels with a mobile darkroom so that results can be immediately processed onsite to generate usable images more quickly. These radiographic inspection capabilities offer the most detailed look inside of industrial equipment and can be used, furthermore, to inspect concrete for subsurface features before drilling, coring, or saw cutting.
Weld Inspections
International Inspection offers each of the above NDE methods — VT, PT, MT, UT, and RT — as a means to investigate the condition of welds. Our field technicians average more than a decade of experience testing welds according to AWS (American Welding Society) and ASME (American Society of Mechanical Engineers) codes. This team has performed weld inspections on a variety of structures for clients ranging from theme parks to municipal bodies.
Positive Material Identification (PMI)
The field team also performs positive material identification (PMI) services to verify the composition of a subject’s metallic components. With the recent acquisition of our Niton XL2 Gold PMI Unit, we are now able to determine the identity of subject materials with great ease. We can perform this method to supplement failure analysis investigations, conclusively establishing whether the material used in manufacture is the same as the metal called out in the design specifications.
Ground Penetrating Radar (GPR)
Finally, our field team can perform ground penetrating radar (also referred to as subsurface interface radar) to locate and image objects beneath the surface of soil or concrete. Hand-held equipment sends radio frequencies through layers of material to bounce off obstacles — good for finding discontinuities ranging from cracks and voids to locating rebar and post-tension cables.
Contact one of our offices today for more information on how International Inspection’s NDE inspection services can help your company.