- Home
- Special Services
MARINE SERVICES
construction
other services
weld services
- NDT Services
methods
additional services
- About Us
- Locations
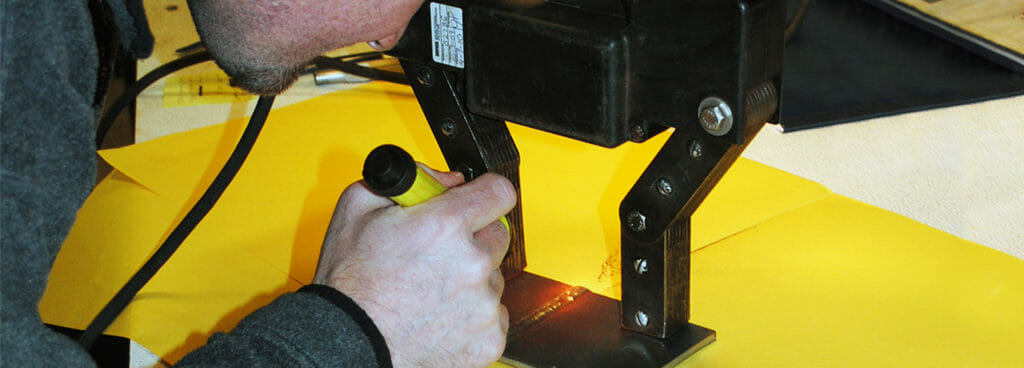
Importance of Effective Welds
International Inspection performs non-destructive weld testing services to clients in a variety of industries. Welding primarily serves to join two or more pieces of metal together in the fabrication or repair process. The welded elements that hold these works together can vary in quality and long-term efficacy depending on the welding procedure and the skill of the welder. Even if the weld itself comes out flawless due to the expertise of the welder, once subjected to stimuli (i.e., cyclic stresses or corrosive environment) in its intended service conditions, eventual failure may be inevitable. Because the structural integrity of important assets such as infrastructure, industrial machinery, vessels, and other structures depends on the continued success of their welded elements, companies understand the need for ensuring their health. International Inspection helps them achieve this through our non-destructive weld testing services.
How We Use NDT to Assess Welds
Non-Destructive Testing, (NDT), is an umbrella term encompassing several methods of analysis that do not permanently change the subject they assess. By using these techniques, International Inspection can determine the condition of welds in two capacities: volumetric and surface inspection to verify the health of a new or in-service weld and examining for defects and conformance as part of a welder qualification test. We perform welder qualification testing in accordance with ASME, AWS, and MIL-STD specifications. Our inspectors, SNT-TC-1A certified as Level II and Level III technicians, perform the following methods to assess the condition of welded elements:
Visual Testing (VT)
The easiest and most immediate way to tell if a weld bears a flaw is by looking at it. Using ancillary tools, such as rulers, straight edges, magnifying glasses, and weld gauges allows inspectors to document critical measurements and evaluate the overall condition of the weld joints. Technicians tend to use this method to preliminarily judge whether further testing is warranted. For instance, if a welding candidate submits a sample coupon that obviously fails the standards of their test based on visible defects, our inspectors do not waste our client’s money examining it with more intensive means. Conversely, they may determine a need for an exhaustive analysis of a visually defective weld on a client site to investigate the extent of the indication and make a more informed recommendation for its repair.
By consulting the criteria outlined in the standards relevant to the type of inspection, our technicians can use visual testing to find a variety of surface-level flaws, such as porosity, cracks, unfilled craters, undercut, root concavity, improper weld height, visible indications of corrosion, and non-conformance with design specifications.
Penetrant Testing (PT)
One of those previously mentioned more intensive testing methods is penetrant testing. Technicians perform PT by applying a special, penetrative dye to the surface of the weld. Natural forces draw the dye into any discontinuities on the weld’s surface, allowing our inspectors to wipe away the excess and leave behind any that seeped into surface discontinuities such as cracks, pores, and the like. By applying a developer that draws the dye back to the surface (and visually contrasts with it), they can easily see those surface discontinuities. Depending on the circumstances of their inspections, our technicians may use either a vivid visual dye or a fluorescent variation viewed under ultraviolet light.
Effective use of PT reveals surface defects smaller than VT can detect — highlighting and contrasting these flaws so that the naked eye can easily pick them out. Beyond the overlap between flaws that both VT and PT in commonly detect (cracks, craters, porosity, etc.) this method especially excels in finding leaks in welds.
Magnetic Particle Testing (MT)
Another technique our inspectors use is called magnetic particle testing. This method takes advantage of the properties of ferromagnetic materials to detect discontinuities at and near the surface. Our inspectors first use a device (a prod, coil, or yoke as appropriate to the inspection) to apply an electric current to the material, which causes it to magnetize. They then apply highly visible, ferrous particles to the surface; these particles congregate at places of magnetic flux leakage, which is caused by flaws in the weld. Their grouping indicates to technicians the size, shape, and location of flaws that run perpendicular to the flow of the magnetic field they generate.
MT allows our inspectors to quickly and easily reveal linear defects — i.e., cracks and seams. This method is suited to finding fractures such as cooling cracks, grinding cracks, quench cracks, and the like. Furthermore, technicians rely on MT to analyze repair welds for efficacy in industrial assets like structures, machinery, and equipment.
Ultrasonic Testing (UT)
A volumetric method, ultrasonic testing lets technicians detect flaws both on and beneath the surface using high-frequency sound waves. By scanning the surface of the weld at a given angle with a transducer, they can send a beam of sound into the structure; it follows a calculated path, bouncing from the base plate to the weld itself. Some of the energy gets reflected at the probe when the sound waves travel along their path — a phenomenon that indicates a change in the material’s continuity or density (i.e., a flaw). This returning sound gets logged as a waveform that indicates the amount of energy detected and how long it took to come back. Due to the complexity of the information, our experienced technicians must interpret the resulting data to determine the location and severity of any flaws detected.
UT allows technicians to find several types of flaws, including stringer inclusions, lamination, incomplete penetration, lack of fusion, and so on. Furthermore, they can use this method to maintain records of material thickness and deduce material loss over time due to corrosion. UT is sensitive enough to pick up defects smaller than those other NDT methods can detect.
Radiography Testing (RT)
Perhaps the most intensive of non-destructive methods used for volumetric weld testing, radiography allows technicians to observe the weld’s internal conditions. Because high-frequency electromagnetic waves (like X-Rays and gamma rays) can penetrate solid matter and be projected onto film, technicians use them to take an image of a subject’s interior. By exposing an Iridium-192 source, focusing and aiming the gamma waves it emits at the weld using a collimator, and detecting the amount energy remaining after it passes through the subject, our inspectors can produce an image of the weld’s interior conditions.
Using this method, technicians can create an actual image of the interior conditions more easily comprehended by the client than interpreting UT presentations. RT proves especially useful for finding voids, slag inclusions, cracks, porosity, lack of fusion, lack of penetration, undercut, concavity, and underfill. Clients can easily review the radiograph or digital image to verify weld integrity.
Positive Material Identification (PMI)
Finally, we also utilize positive material identification in weld testing. One of the important factors contributing to a weld’s success and long-term efficacy is the use of appropriate filler material; selecting an incompatible filler material will make the product susceptible to failure. Our technicians use a handheld X-Ray fluorescence (XRF) unit to determine the alloy and chemical composition of the filler metal used in a weld.
If your company needs non-destructive weld testing services, either as part of a larger inspection or to validate a welder’s qualifications per applicable standards, contact International Inspection today. Our inspectors have cumulative decades of experience using the above NDT methods to assess the condition of welds both accurately and efficiently.