- Home
- Special Services
MARINE SERVICES
construction
other services
weld services
- NDT Services
methods
additional services
- About Us
- Locations
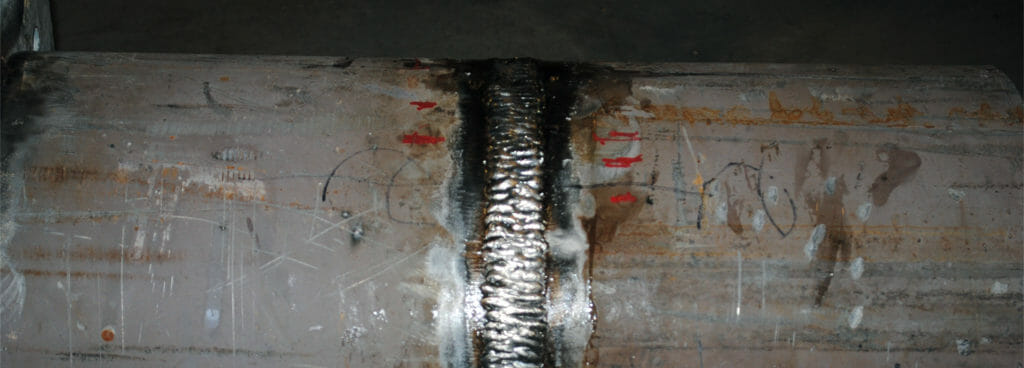
Benefits and Applications of Inspecting Welds
International Inspection performs welding inspection services using several nondestructive testing methods to determine the efficacy of a welded element. We do this because not all welds are created equal; some come with defects (e.g., slag inclusions, incomplete penetration, cracks, porosity, undercut, voids, etc.) that result from not adhering to weld specifications. These imperfections can undermine the structural integrity or life-expectancy of a fabrication. Our certified inspection professionals bring cumulative decades of experience detecting and characterizing the flaws that can occur in weldments.
Companies typically request a welding inspection for one of two reasons: as part of a larger assessment of an industrial asset’s continued viability or to certify a welder’s competence performing a certain welding procedure. International Inspection performs both applications.
Welder Qualification Testing
Clients request welder’s performance qualification testing when they need a welder assessed. Our welding inspectors will analyze their sample coupon for several types of flaws — those immediately visible and those lying beneath the surface. By detecting and characterizing any present defects, these experts can assess how closely the candidate followed the necessary procedures. If their weld proves code-compliant, International Inspection will affirm their competence in the given welding technique. We assess candidates according to the AWS, ASME, and famously stringent MIL-STD codes.
Onsite Inspections
When requested in the inspection scope, our technicians can assess welded elements of clients’ industrial assets according to relevant codes as a component of a given onsite inspection. Our inspectors look for any indications of damage, corrosion, or thickness loss that occurred as a result of anticipated service conditions. They lay out their findings in a report that guides clients on any recommended preventive maintenance or repairs they must perform on the subject they examined. When their evaluation determines that an area of concern must be repaired by welding, they can even verify that the repair has been completed to code and does not bear any unacceptable flaws.
Nondestructive Testing
Our technicians perform every welding inspection service using one or more methods of nondestructive evaluation (NDE). Also referred to as nondestructive testing (NDT), this umbrella term covers industrial methods of analysis that do not cause any lasting change to the subject they examine. Every member of our field inspection team maintains certification as a Level II or a Level III inspector in accordance with SNT-TC-1A. We use the following methods in our welding inspections:
- UTT (Ultrasonic Thickness Testing)
- UTSW (Ultrasonic Shear Wave Testing)
- Leak Testing
- MT (Magnetic Particle Testing)
- RT (Radiographic Testing)
- PMI (Positive Material Identification)
- Hardness Testing
- Vacuum Box Leak Testing
Our inspectors perform the above methods per applicable weld assessment codes, including those of the American Society of Mechanical Engineers (ASME), the American Welding Society (AWS), and military standard specifications (MIL-STD).
Defects We Regularly Detect in Weldments
Welding defects can occur at nearly any point in the welding process. While some bad welds are immediately visible, others may hide flaws that are too minuscule for the naked eye to perceive or that lie below the surface of a seemingly fine weld. Our inspectors regularly find these welding defects during their assessment:
- Cold Cracks
- Hot Cracks
- Incomplete Penetration
- Porosity
- Lack of Fusion
- Leaks
- Slag Inclusions
- Stringers
- Surface Cracks
In case of in-service components, our welding inspectors specifically search for signs of cracking and corrosion, which disproportionately affect welded elements. Not typically caused by an improper welding technique, corrosion can set in during regular service conditions as it is a byproduct of nearly unavoidable environmental agents. International Inspection’s team of field technicians can locate visual indications of corrosion on the surface during their initial inspection, but these observations may not paint the whole picture; often they need to use a more intensive NDT method, like UT, PT, MT, or RT to determine the extent of the damage.
If your company needs a trusted provider to qualify their welding candidate or to assess weldments as part of a larger inspection, contact International Inspection today. Our welding inspection services can serve your specific needs.