- Home
- Special Services
MARINE SERVICES
construction
other services
weld services
- NDT Services
methods
additional services
- About Us
- Locations
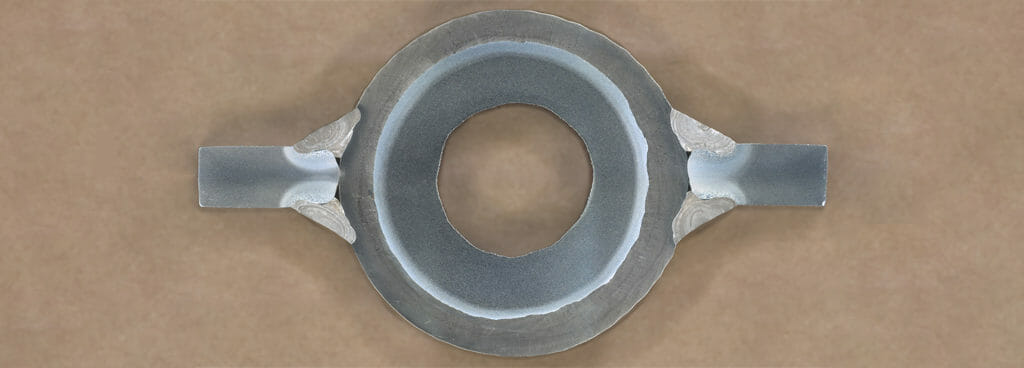
Our Weld Inspection Services
International Inspection performs weld inspection services for clients from a variety of industries. Every fabricator knows that the structural integrity of their final product primarily depends upon the quality of the welds used to hold it together. Not following properly qualified welding procedures often results in a weld of subpar quality, which can increase the fabrication’s likelihood of failure under intended service conditions. By inspecting for defects, our technicians can help clients ensure that their welds meet relevant standards of quality assurance. We perform this service in two capacities:
- Onsite Inspections
- Welder Qualifications Testing
Onsite Inspections
Our field technicians can inspect the condition of weldments in client assets according to a variety of codes while onsite. These professionals check for proper weld sizes, indications of flaws, defects, and damage to welded elements. They then draft a report on their observations, which clients can use to inform any preventative maintenance or repair actions they undertake to uphold the viability of their assets.
Welder Qualifications Training
When a client wants someone tested for competence in performing a given weld procedure, International Inspection can help them assess their candidate’s abilities. Our experts examine welded test coupons for visual defects and subsurface flaws — characterizing its code compliance and determining its long-term effectiveness in a service setting. International Inspection examines candidates according to ASME, AWS, and the rigorous MIL-STD codes.
Nondestructive Weld Assessment Methods
We perform these services using a variety of nondestructive testing (NDT) methods. Our technicians are certified by the American Society of Nondestructive Testing (ASNT) to conduct examinations of client structures, equipment, and machinery using the following assessment methods:
The team performs this testing in accordance with relevant codes, such as American Welding Society (AWS), American Society of Mechanical Engineers (ASME), and Military (MIL-STD) standard specifications.
Commonly Encountered Weld Defects
By using the above disciplines of nondestructive testing, we can detect several types of flaws in welded elements. These defects can arise for a range of reasons, and one or more can occur at almost any point in the welding process. Even clean-looking welds can hide problems beneath the surface that compromise its strength and effective lifespan. These are the flaws we find most often in our evaluations:
- Lack of Fusion
- Surface Cracks
- Porosity
- Incomplete Penetration
- Hot Cracks
- Cold Cracks
- Stringers
- Slag Inclusions
The field team is also vigilant in checking for evidence of corrosion on client assets. While not a condition resulting from the lack of adherence to a proper welding procedure, weldments remain more susceptible to this kind of gradual environmental damage than surrounding parent materials. Inspectors can catch surface indications of corrosion in their visual assessment but may require a more intensive test to profile the scope of the damage. Any corrosion located beneath the outside surface of a given weldment, such as inside a section of piping, is detected using RT, UT, MT, or PT.
If your company needs weld inspection services from a trusted provider, contact International Inspection, Inc. today. Our expert technicians can meet your specific needs.